CAD-to-CAM Optimization of Modular Campervan Furniture Kits
Parametric design and manufacturing refinement for modular plywood furniture systems, integrating SolidWorks CAD with CNC toolpath development in VCarve Pro.
This project involves reverse engineering and redesign of modular flat-pack furniture kits used in campervan conversions. Starting from existing 2D layouts, I developed 3D CAD assemblies, introduced joinery improvements, and applied DFM/DFA principles for easy manufacturing, error-free assembly, and CNC compatibility. Toolpath generation and nesting optimization were performed in VCarve Pro to reduce rework, prevent tool breakage, and streamline production on-site.
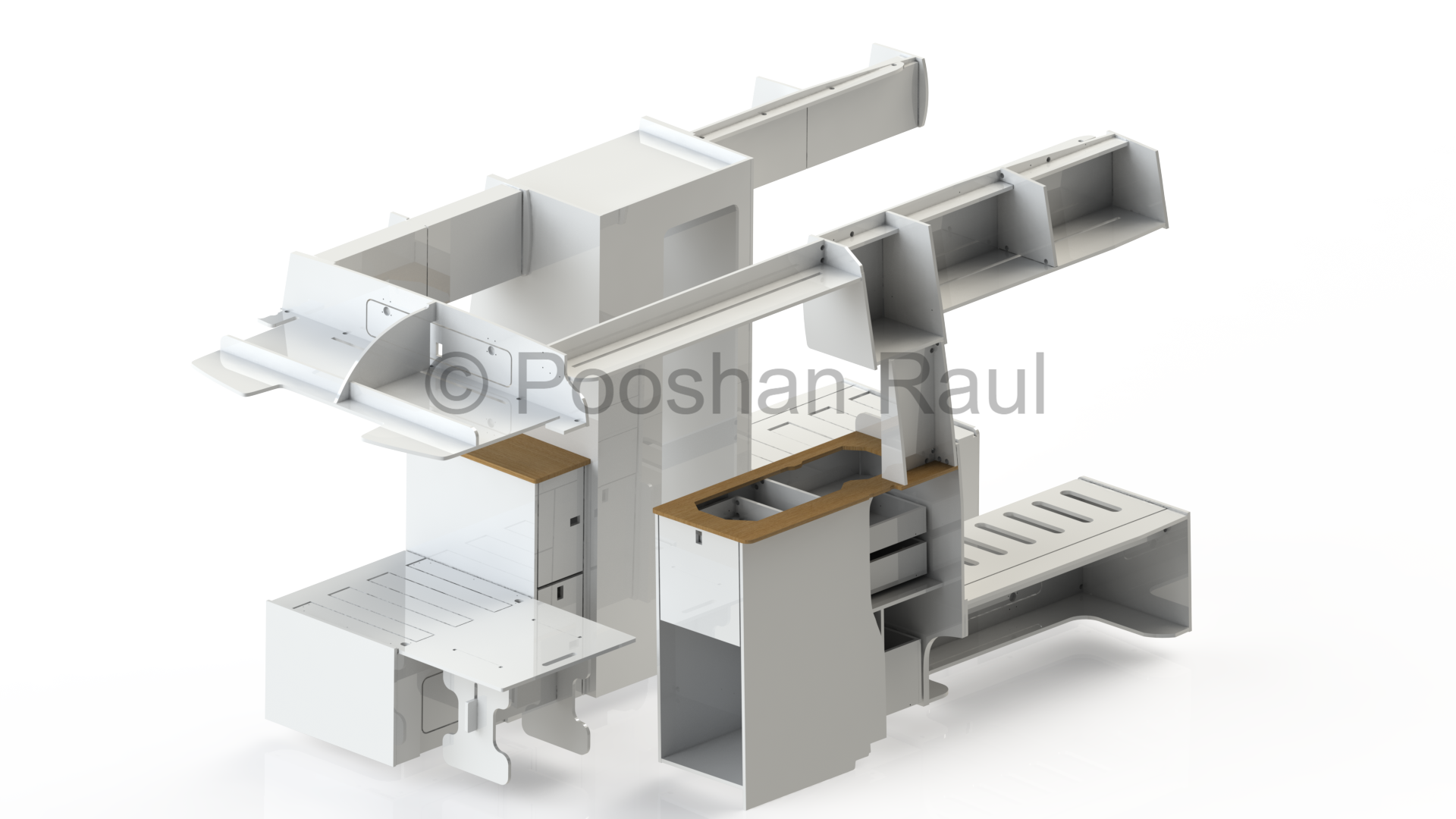
Remastering Legacy Kits
Flat-pack DXF outlines were imported into SolidWorks to reconstruct fully constrained 3D assemblies. This allowed for parametric control, spatial validation, and further optimization based on client-specific requirements.
- Converted 2D DXFs into 3D part models and assemblies
- Mates and references defined for feature consistency
- Assembly layouts validated for fitment inside vehicle interiors
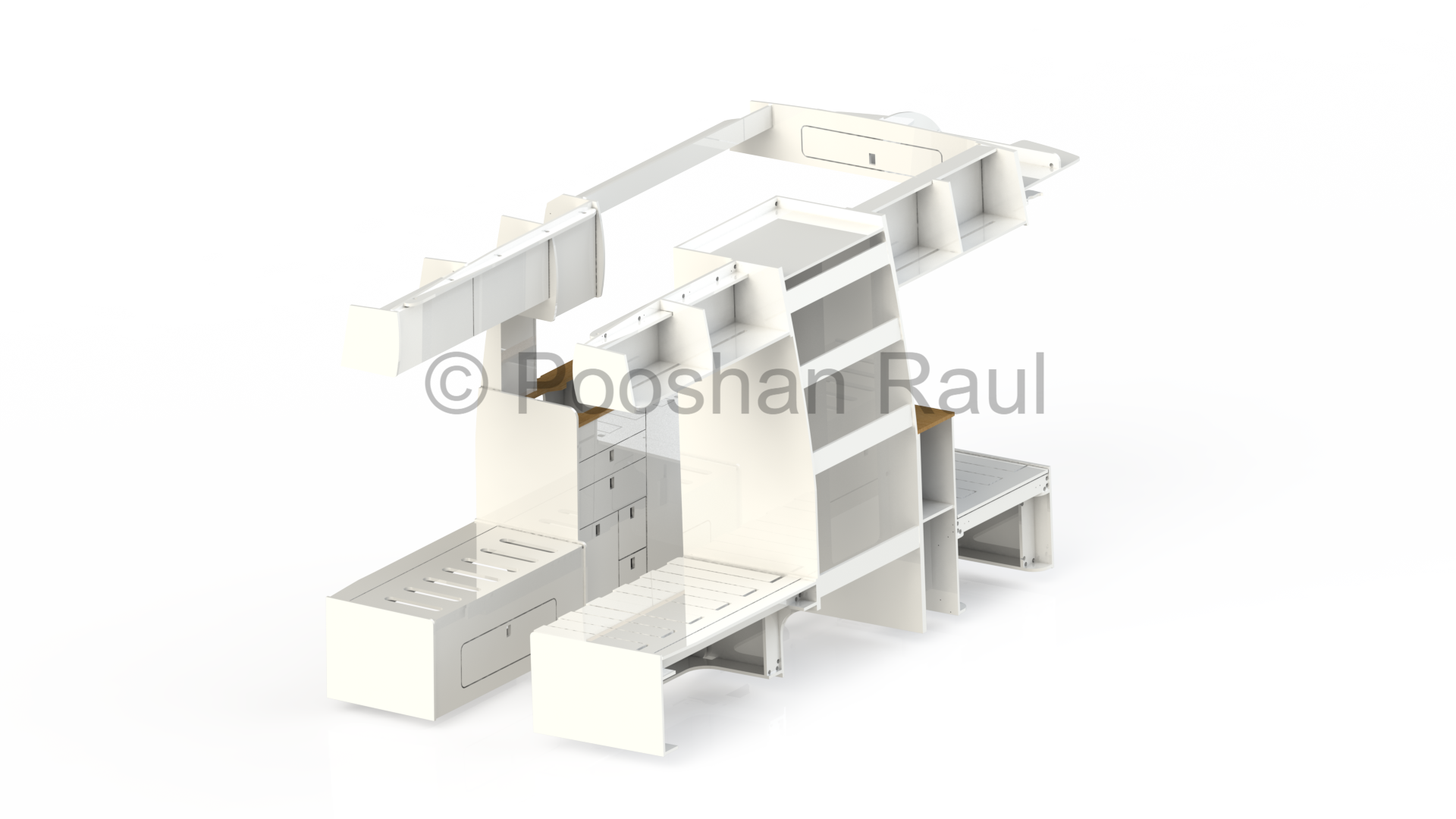
Modular Layout Adaptation
Designed modular furniture kits tailored to long and mid-wheelbase variants of VW vans. Subassemblies for kitchens, beds, and storage were adapted into interchangeable formats, ensuring structural compatibility across layouts.
- Functional modules derived from a master sketch base
- Kits adapted to vehicle hardpoints and volumetric constraints
- Design constraints applied to simplify reconfiguration across models
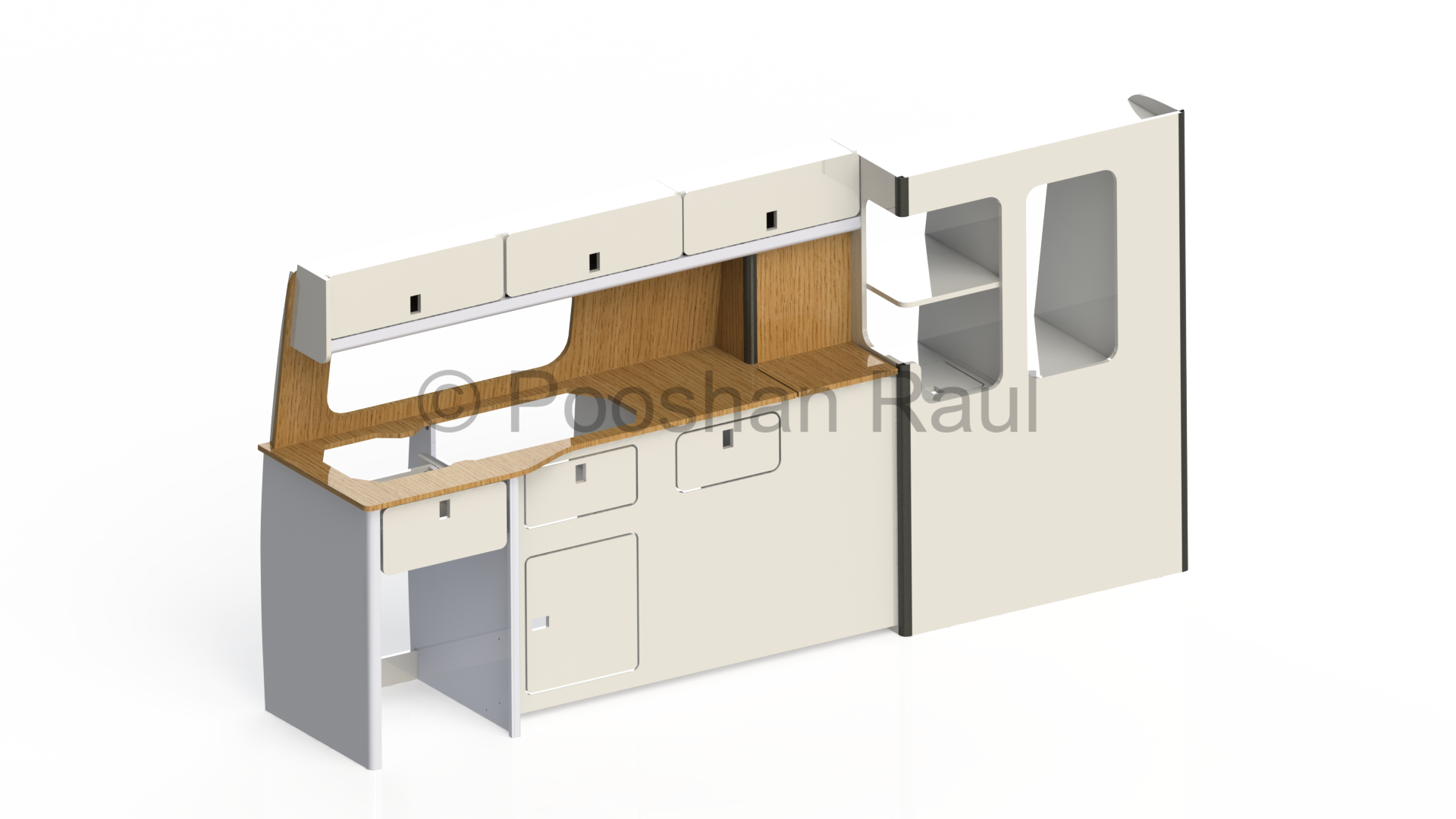
Joinery and Assembly Optimization
Features were added in SolidWorks using DFM/DFA principles to support clamp-free, tool-free assembly. Joinery was tuned for precision fit, alignment, and strength — ensuring both structural rigidity and manufacturing ease.
- Cam-lock, slot-fit, and interlocking features added parametrically
- Edge treatments introduced to ease self-alignment during build
- Reinforcements added to withstand road-induced vibrations
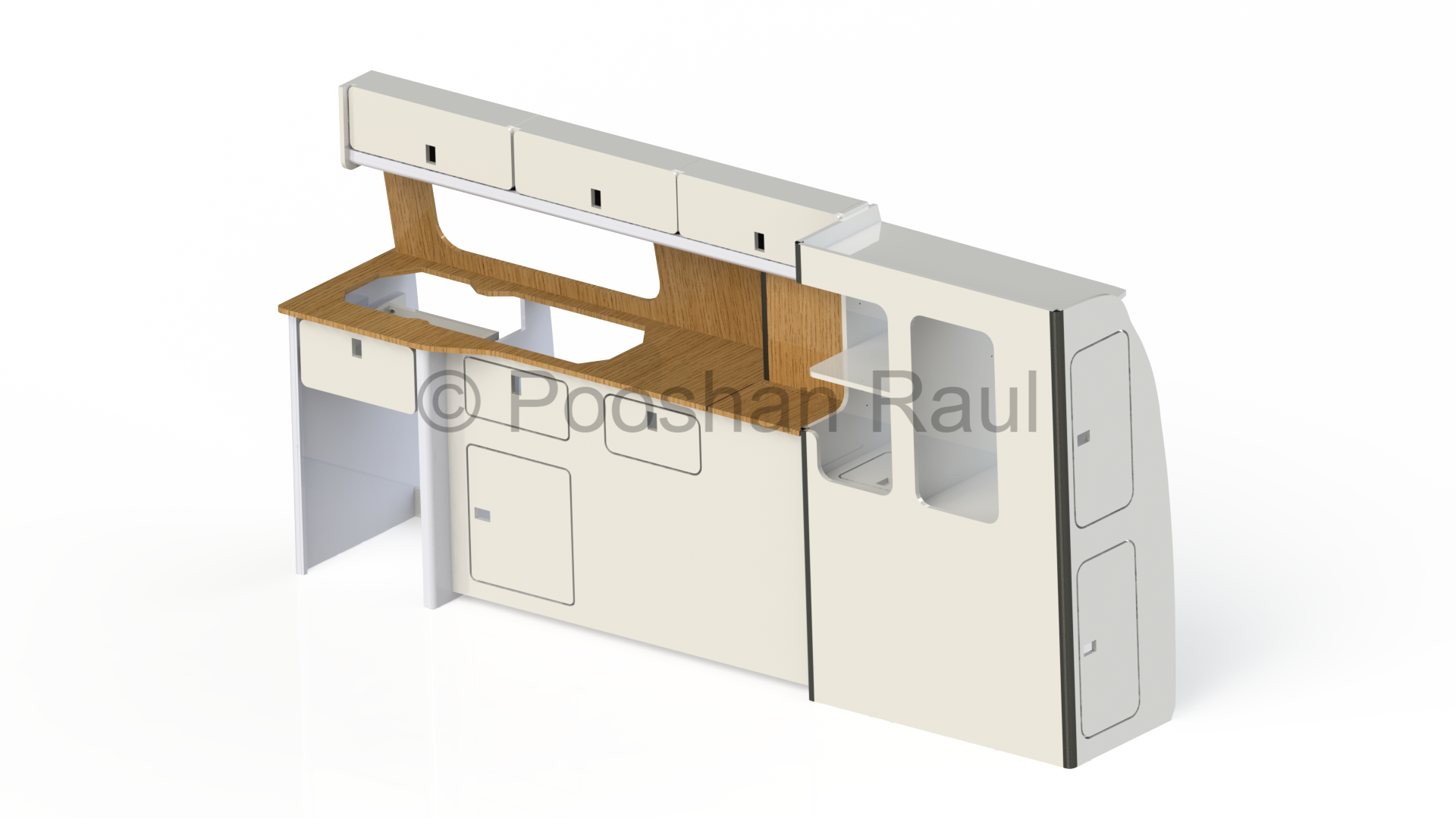
CAD Preparation for CNC Routing
The finalized 3D parts were exported back to 2D DXFs for manufacturing. Each panel was designed to conform with standard sheet sizes (2440 × 1220 mm) and optimized for CNC compatibility through careful grain orientation, slot relief, and edge clearance.
- Tab-and-slot geometry adjusted for 18mm birch plywood tolerances
- Grain-safe layouts designed to reduce tear-out and improve finish
- CAD validation included edge clearances and fitment allowance prior to nesting
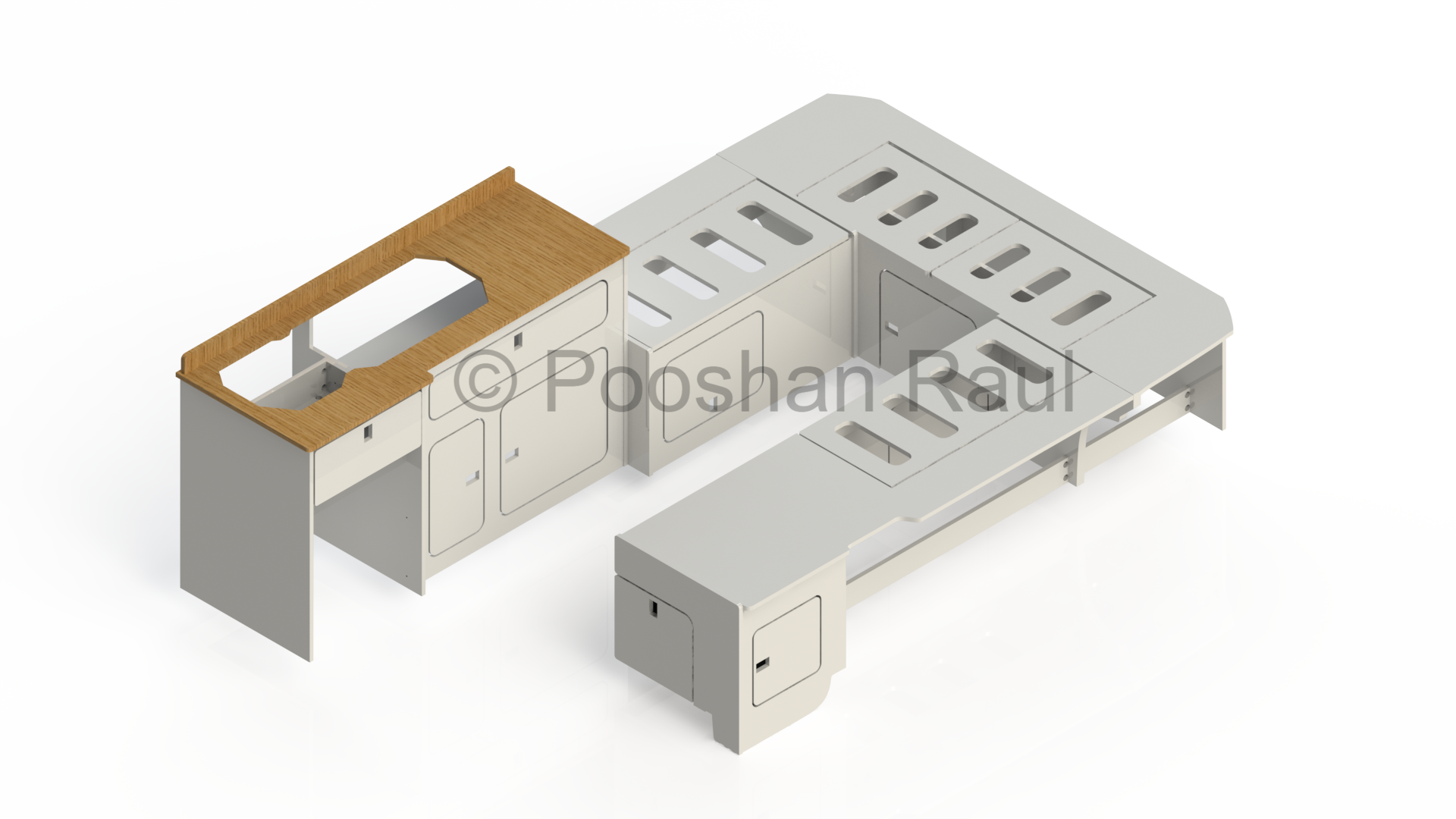
CNC Tooling Strategy
A compression bit was used to eliminate tool swaps between upcut and downcut bits, reducing machining complexity. Separate cutting strategies were used for birch plywood and bamboo (used in kitchen tops) based on their density and chip behavior.
- Compression bit ensured clean top/bottom finish on plywood
- RPM and feed rates tuned specifically for bamboo vs birch
- Machining depth/passes adjusted to prevent delamination and overheating
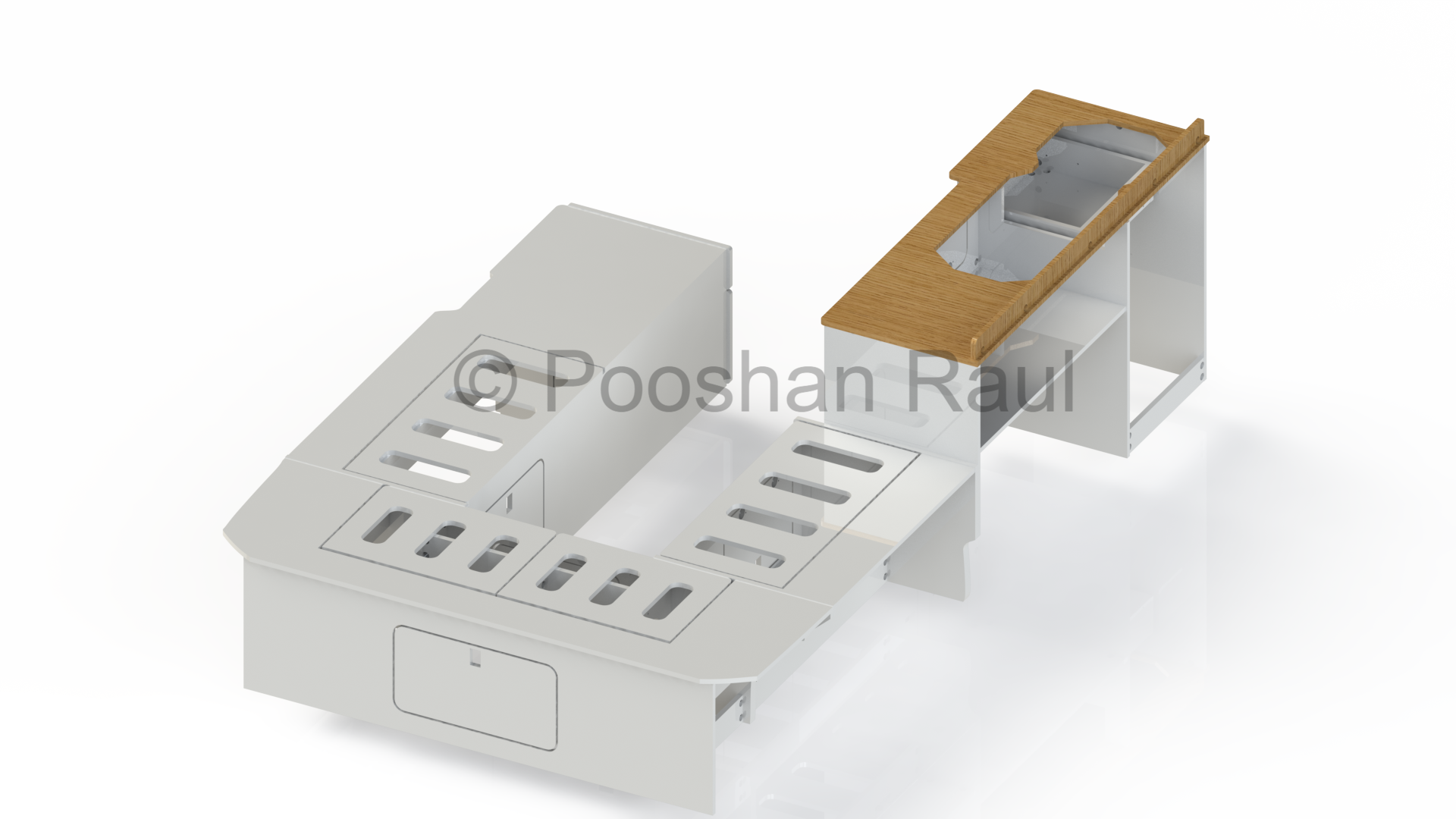
Toolpath Template Setup in VCarve Pro
Parts were processed in VCarve Pro using standardized toolpath templates for repeatable CNC programming. Instead of dry runs, thin plywood sheets from packaging were used to create template test cuts for physical fitment trials without wasting raw material.
- Reusable VCarve templates created for pocketing, profiling, and engraving
- Fitment-tested using scrap packaging ply for template validation
- Part engraving used to ensure orientation and part ID during assembly
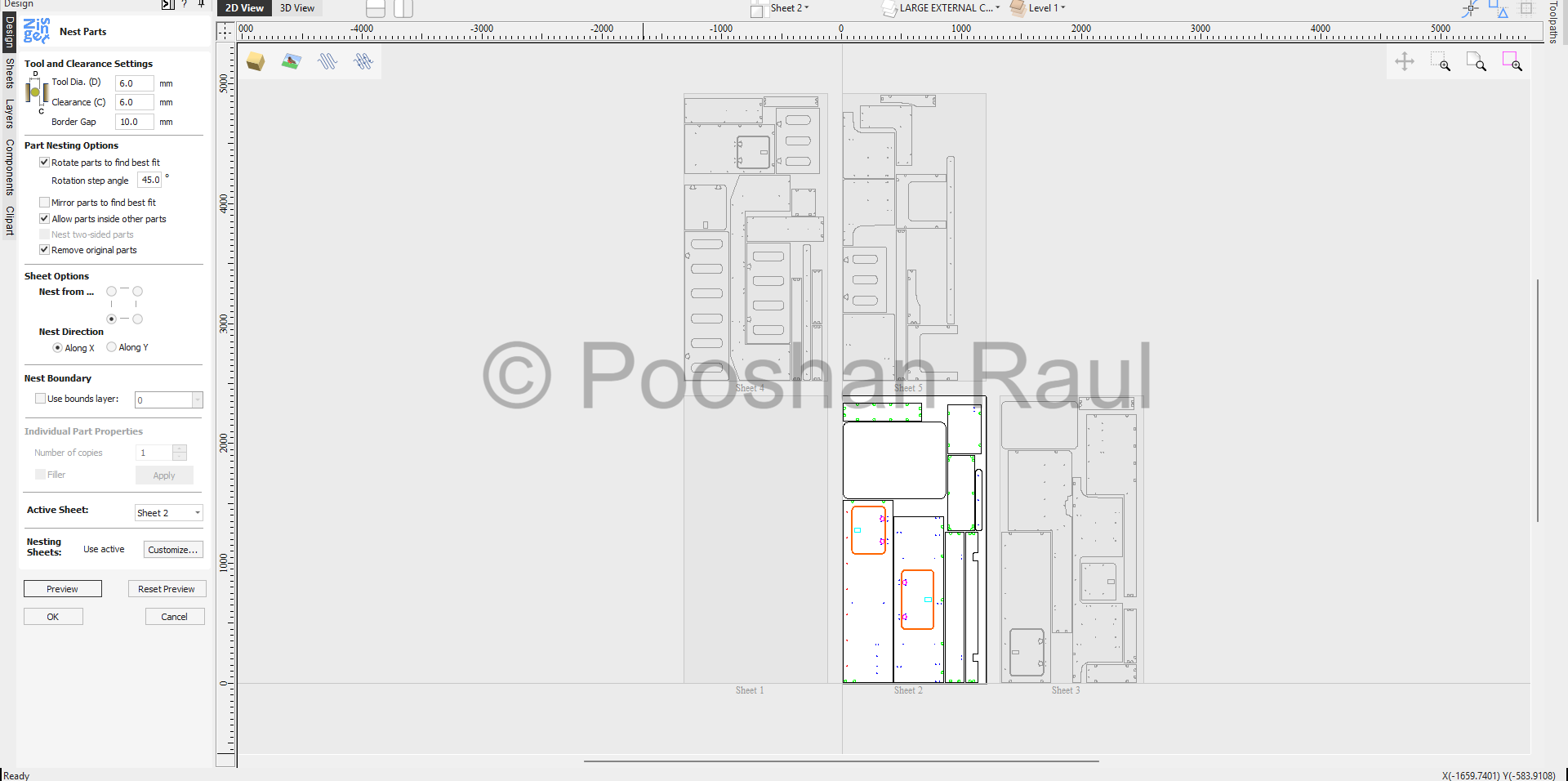
Outcome and Field Testing
The kits were successfully machined, assembled, and installed without rework. On-site feedback confirmed improved dimensional accuracy, faster build cycles, and better durability during on-road testing.
- 90% reduction in manual post-processing
- Toolpath strategy validated through multiple production batches
- All kits passed vibration and rattle checks in real vehicle environments
End-to-End CAD to Manufacturing Workflow
Each campervan furniture kit followed a consistent and validated engineering pipeline:
Flat-Pack DXF → Parametric 3D Modeling in SolidWorks → DFM/DFA Joinery Optimization → DXF Export → VCarve Pro Toolpath Templates → CNC Manufacturing → Test Fitment & Field Installation
This workflow enabled production-ready outputs with repeatable quality, minimized rework, and fast assembly turnaround — tailored for both custom and batch manufacturing.
Project Information
- Project Date: Ongoing (2024–Present)
- Software: SolidWorks, VCarve Pro
- Category: Modular Furniture Design & Manufacturing
- Focus Areas:CAD Remastering, Joinery Design, Toolpath Automation, CNC Process Tuning