Modelling of Novel Heat Pipe Design using ANSYS Fluent
Validation of a lithium-molybdenum heat pipe design under fusion-relevant thermal loads using CFD and cross-comparison with COMSOL data.
This project explores the thermal performance of a molybdenum-lithium heat pipe under fusion-relevant conditions. A reduced-order 2D axisymmetric CFD model was developed in ANSYS Fluent and validated against benchmark results from COMSOL (TU/e). The goal was to simulate lithium phase-change cycles and assess thermal gradient distribution in a simplified geometric domain.
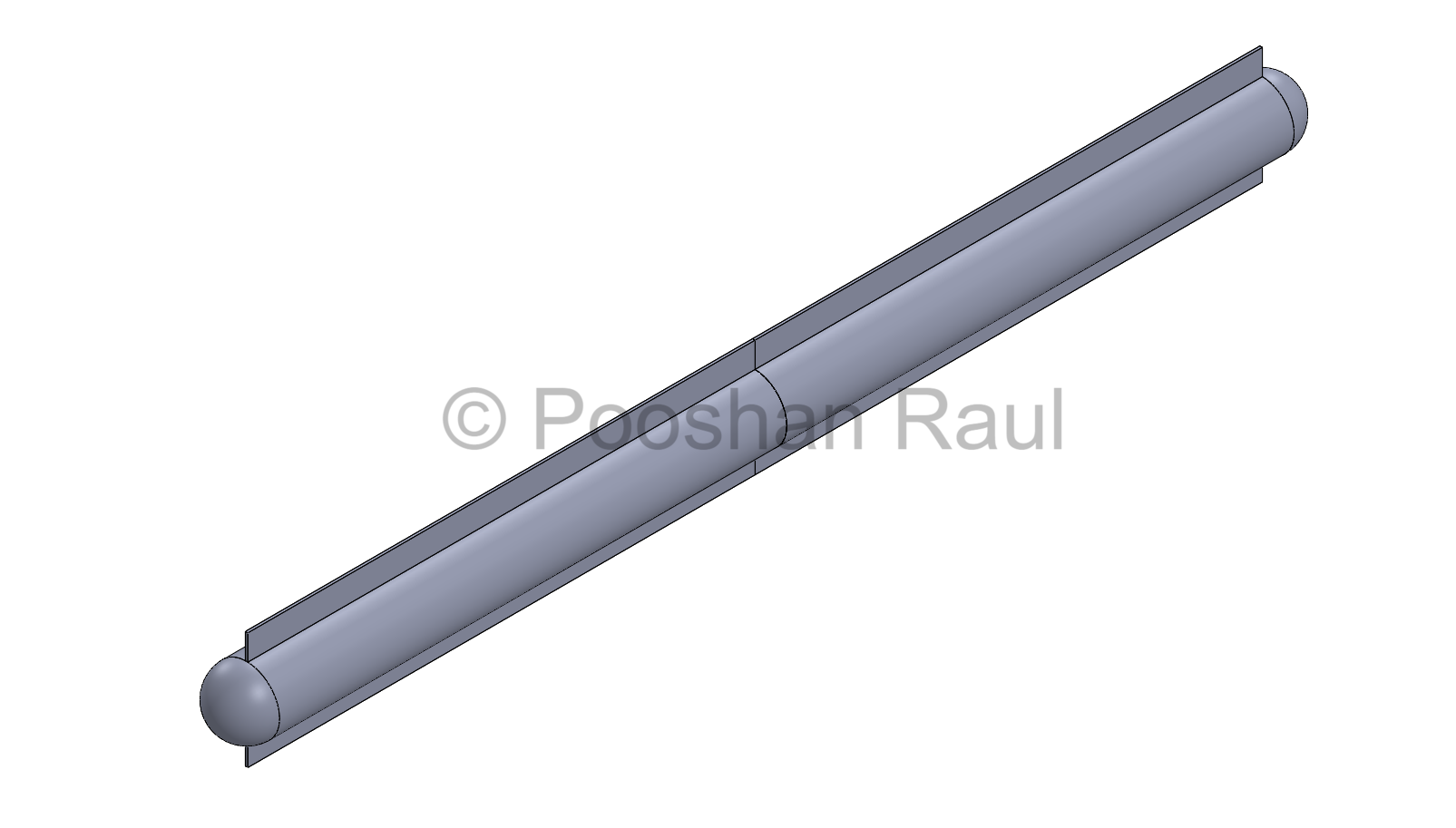
Novel Heat Pipe
The heat pipe is essentially made form 3D printed molybdenum and has internal capillaries lined with lithium. This structure is designed to sustain heat fluxes upto 20MW/m2, resembling to conditions in tokamaks.
- The pipe works on evaporation condensation cycle of liquid lithium
- The pipe are vacuum sealed for preventing any oxidation
- This heat pipe construction is capable of sustaining upto 2000°C
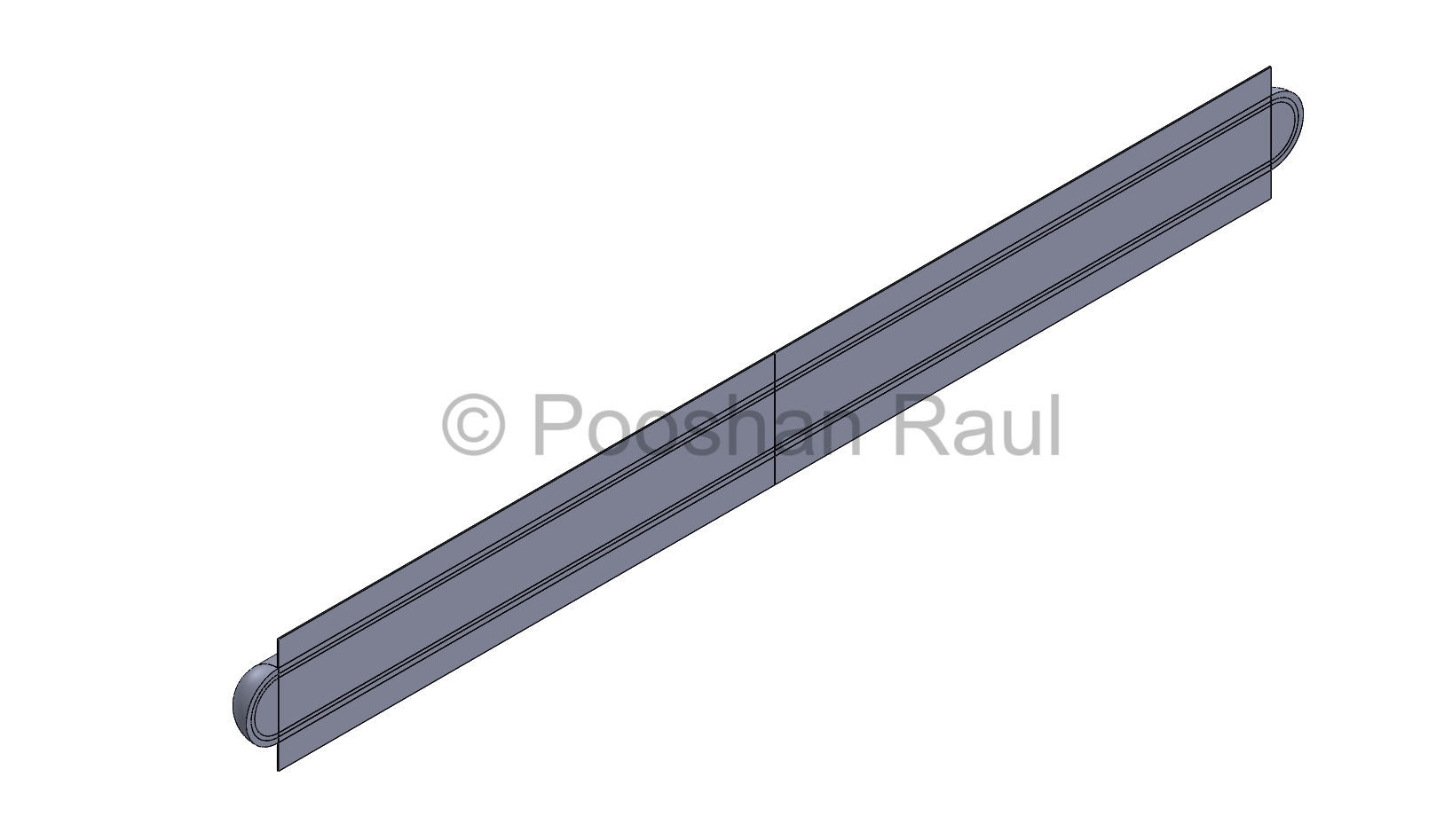
Working Principle
Heat is absorbed at the evaporator region causing lithium to vaporize, and is transported to the condenser end where it recondenses via capillary action. This closed-loop mechanism drives thermal transfer without external flow assistance.
- Vaporization at hot end: ~1600 K peak under high heat flux
- Passive capillary condensation mechanism
- No mechanical pump or active components involved
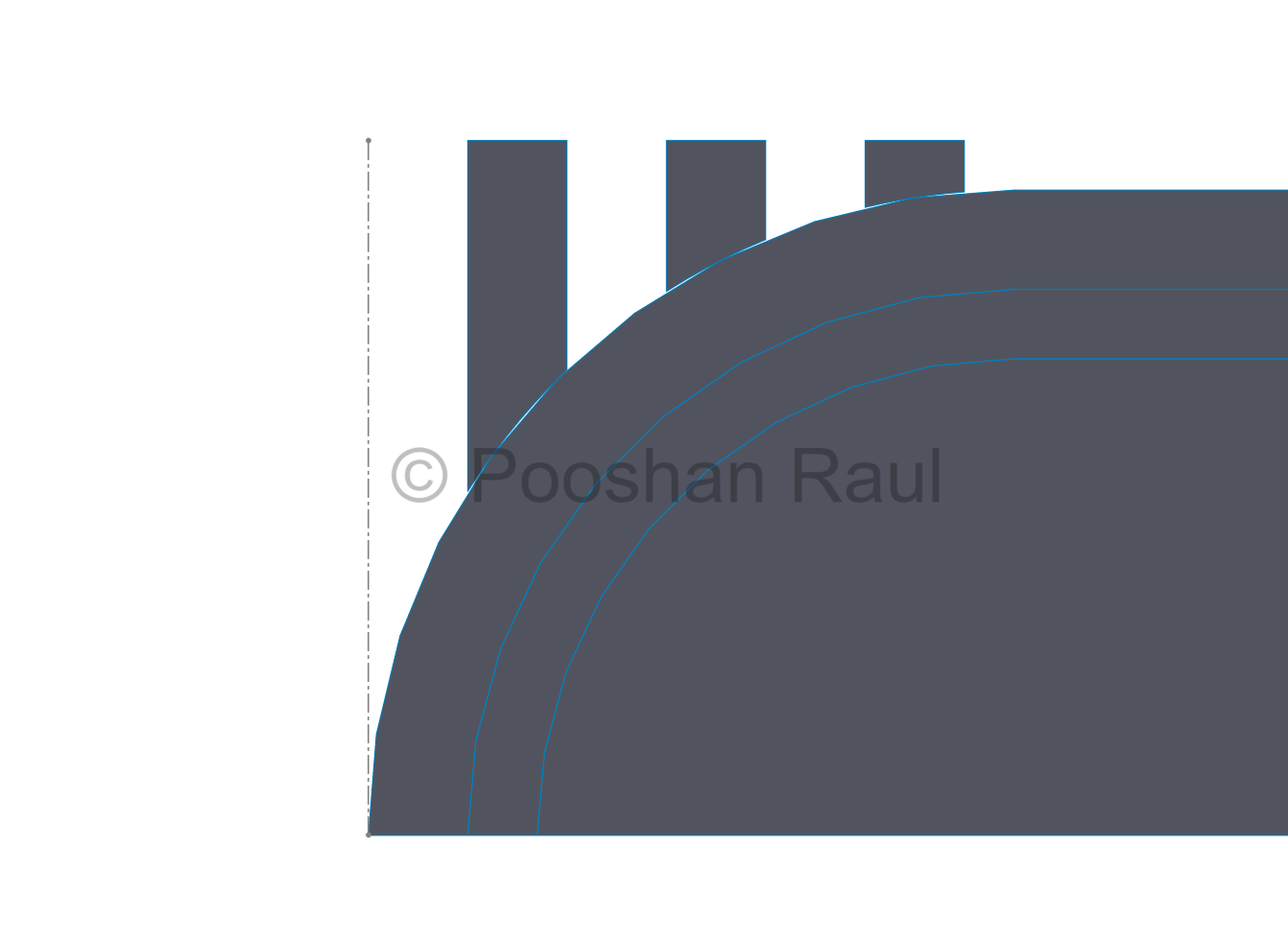
Problem Idealization
To reduce computational cost while preserving physical accuracy, the heat pipe was modeled as a 2D axisymmetric domain. The solid, liquid, and vapor regions were explicitly defined, and multiphase modeling was enabled using the VOF approach.
- Axisymmetric geometry reduced element count
- Multiphase zones defined explicitly for thermal interaction
- VOF model applied to capture vapor–liquid interface dynamics
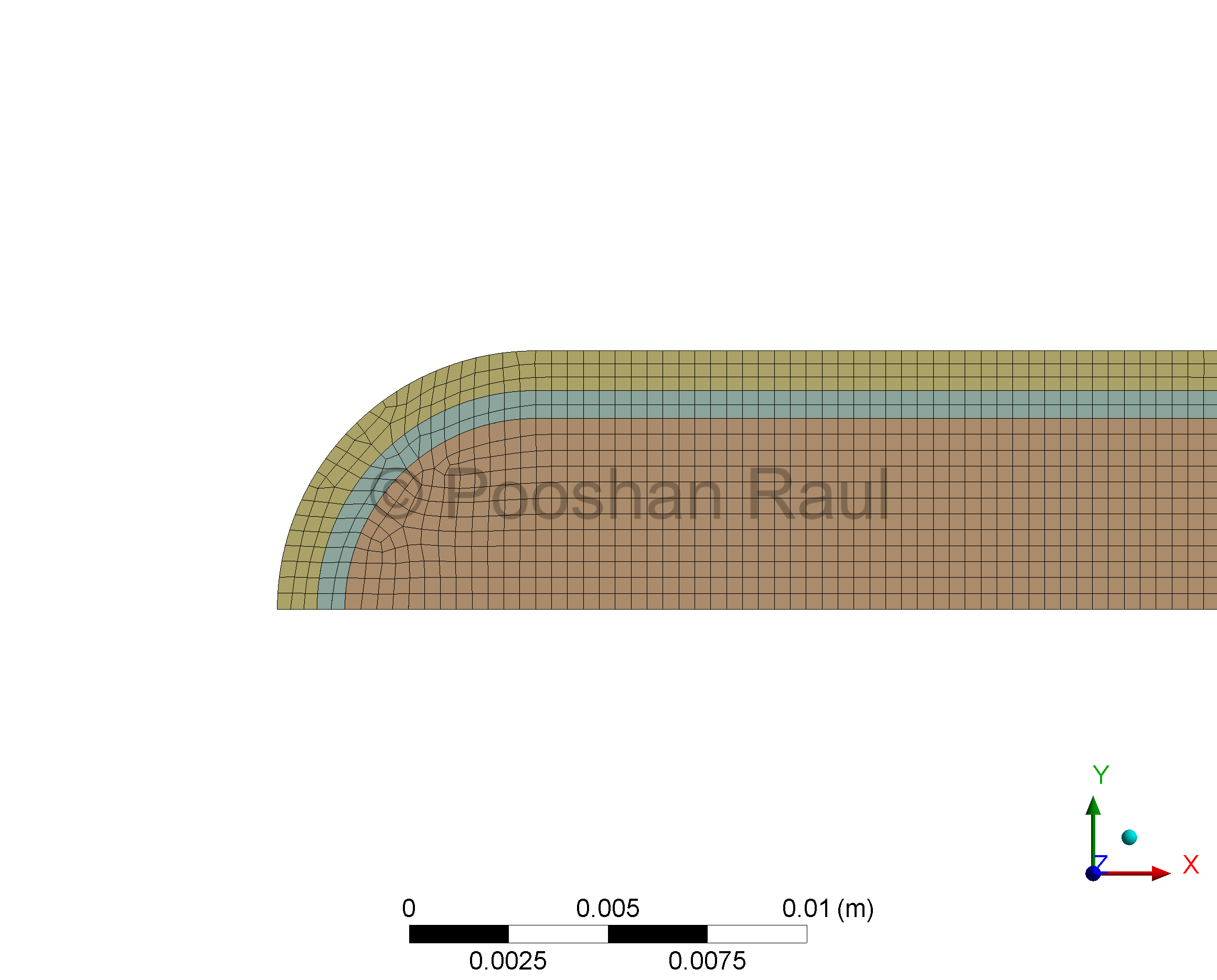
Mesh Refinement & Quality
High mesh quality was ensured to avoid solver instability and increase simulation reliability. Local refinement was applied near the evaporator region where gradients were highest.
- Quadrilateral meshing with 0.4 mm refinement near hot zones
- Skewness ~0.32, orthogonality ~0.74
- No negative volumes or distorted elements observed
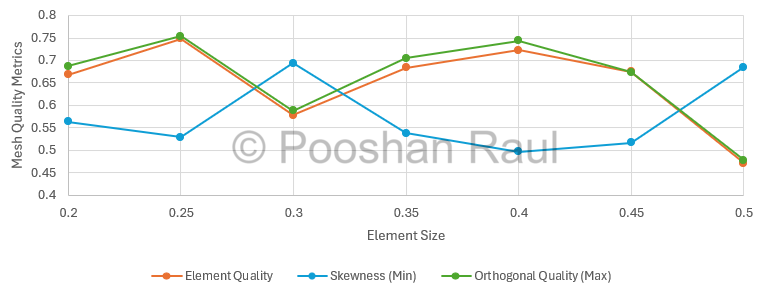
Mesh Metrics
Standard Fluent mesh metrics were evaluated and met convergence safety margins. The mesh was optimized using gradient smoothing and quality checks.
- Aspect ratio < 3 maintained throughout
- Smoothing applied to eliminate stress risers/li>
- Clean topology enabled consistent solver initialization
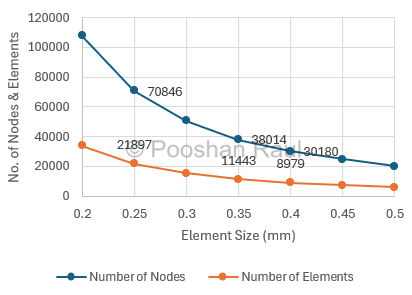
Mesh Convergence Study
A mesh size of 0.4 mm was selected, resulting in approximately 8,500 elements. This configuration provided an optimal balance between mesh quality and computational efficiency, with improved element skewness and acceptable solver runtime.
- focussed on optimum balance between the simulation process and convergence.
- Grid convergence index within acceptable tolerance
- Final mesh used for all thermal post-processing
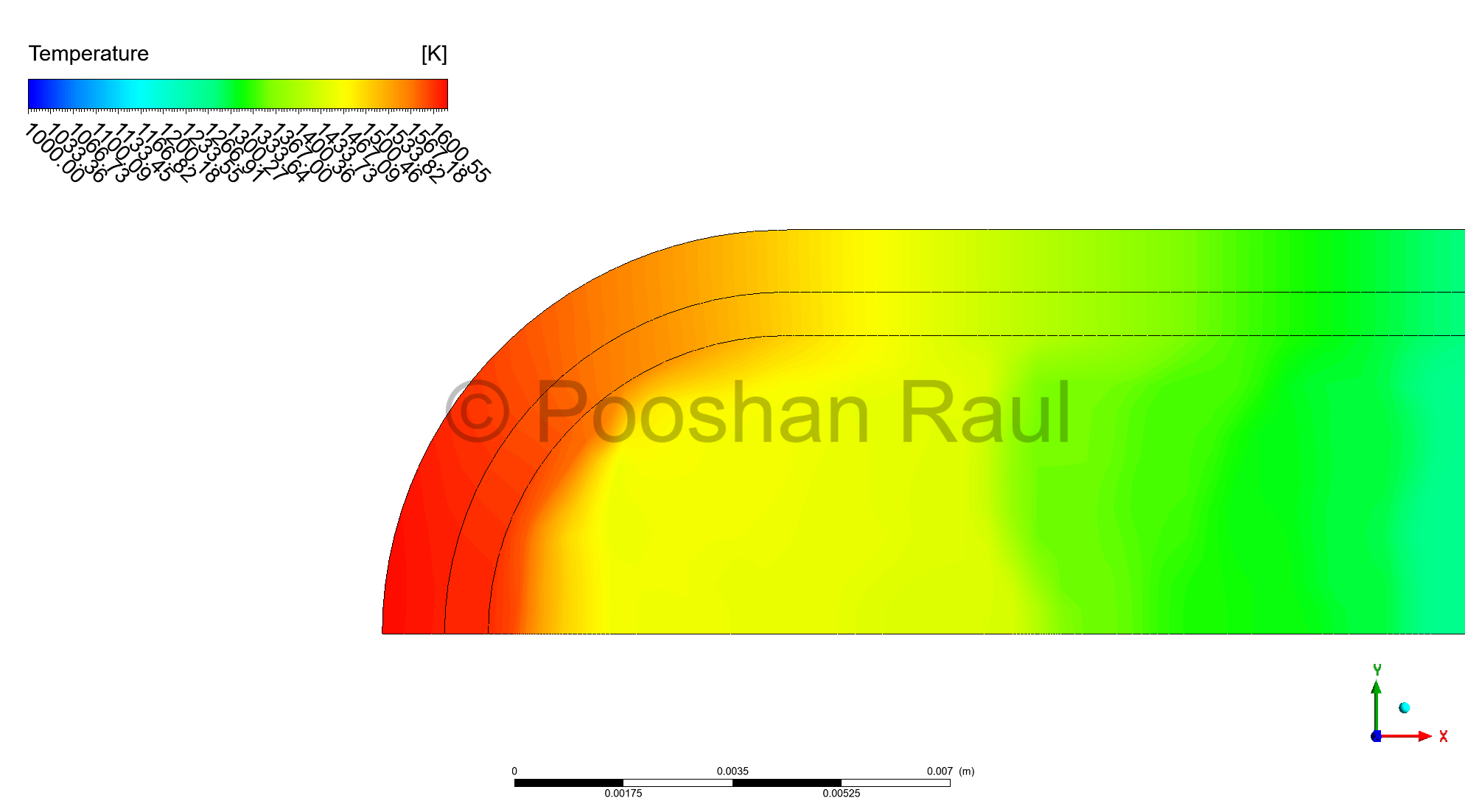
Temperature Results
Peak surface temperatures (~1600 K) matched reference COMSOL data from TU Eindhoven.
- Localized peaks at evaporator edge and mid-wick
- Stable axial drop toward condenser confirmed
- Temperature tracking over 12.3 s of transient simulation
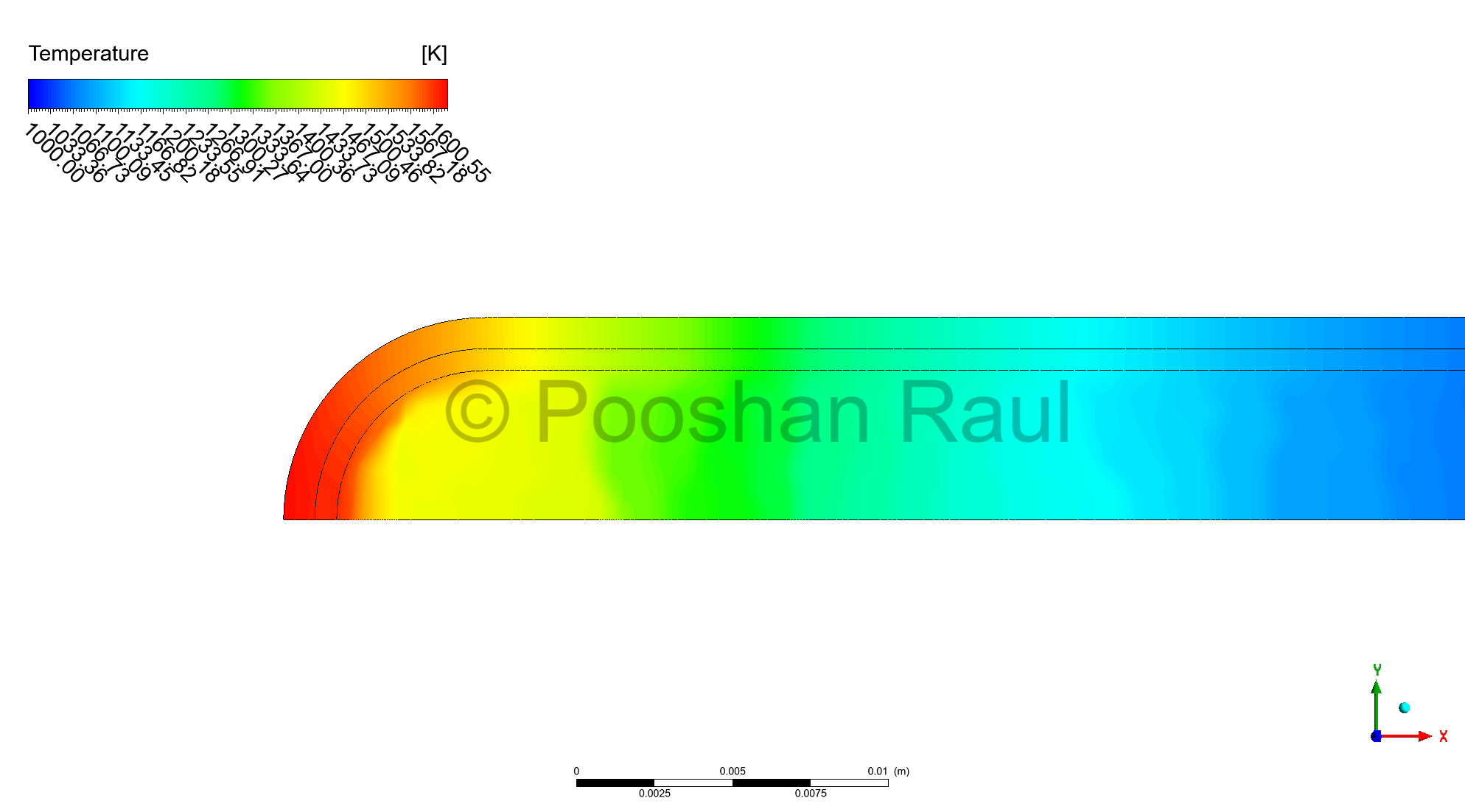
Cross-Validation
Temperature field matched benchmark thermal data despite simplified phase boundaries.
- Minor deviation near liquid-vapor interface
- Axial and radial distribution trends consistent
- Validated without full VOF model implementation
Conclusion
This study validates reduced-order CFD modeling for fusion-grade heat pipe performance. Future work includes multiphase VOF refinement, UDF-based flux inputs, increasing the accuracy of the fluid fluid interface and the solver robustness, and electromagnetic coupling via MHD modules.
Project Summary & CFD Workflow
A novel heat pipe geometry was simulated for use in fusion applications. Axisymmetric simplification reduced computational demand while retaining heat transfer accuracy. The Fluent model was validated against benchmark COMSOL results, demonstrating good thermal correlation despite phase simplification.
SolidWorks Geometry → 2D Domain Setup → insering Temperature dependent materail properties → Mesh Quality Checks → Thermal Load Simulation → Fluent Post-Processing → COMSOL Cross-Validation
Project Information
- Project Date: August 2024
- Software: ANSYS Fluent, SolidWorks
- Category: Research & Development
- Focus: Fusion, Thermo-fluid Simulation, Heat Pipe Design
Let's Connect!
Feel free to reach out to me via Email or LinkedIn.